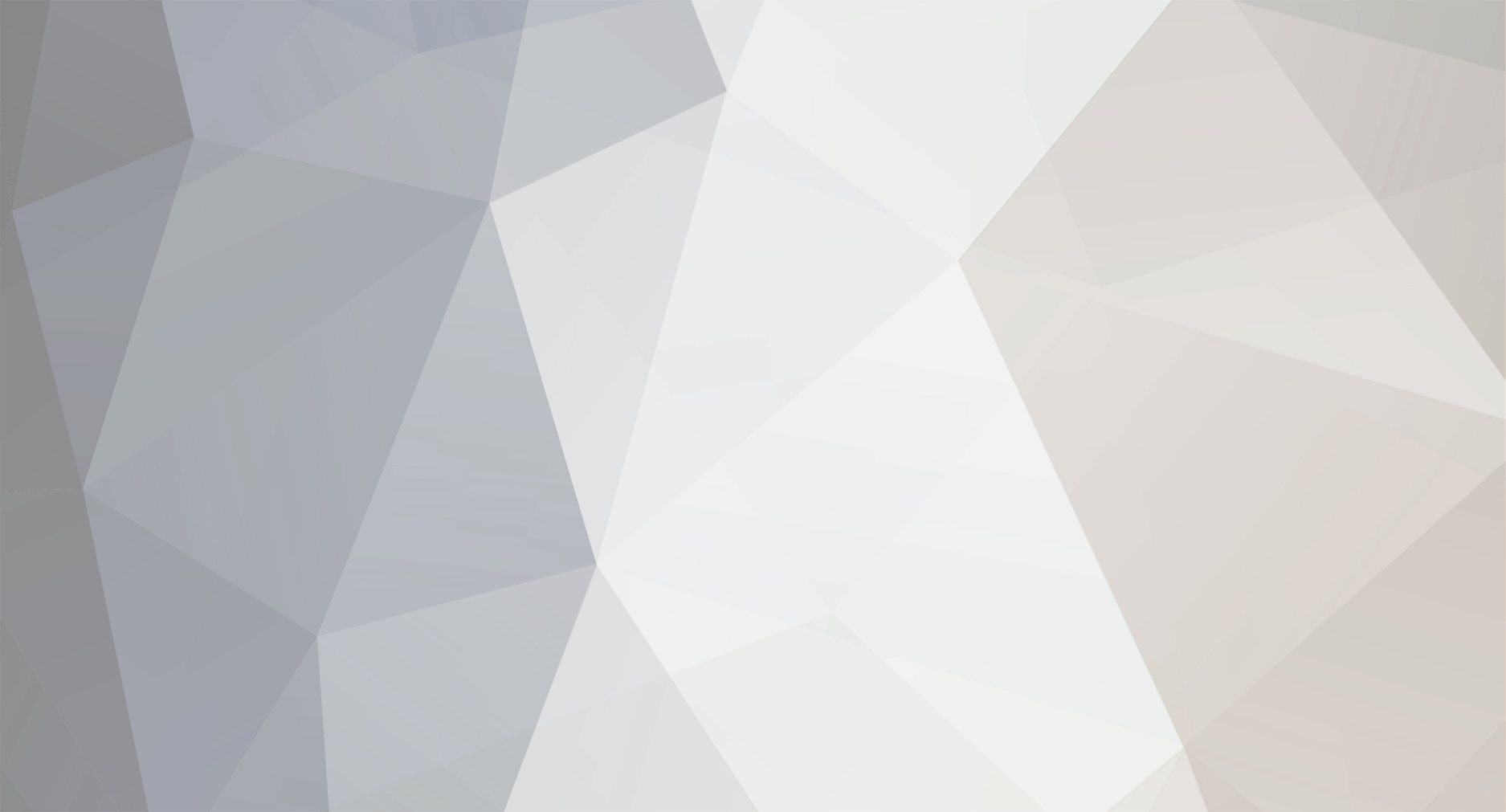
Mark L
AOAI Forum Members-
Posts
177 -
Joined
-
Last visited
Content Type
Profiles
Forums
Events
Everything posted by Mark L
-
Doing some research, I went to the Nostalgic Motor Cars website to see if Dan Booth is advertising any Avanti II cars for sale. He's currently selling a 1982 and a 1983. Both have defroster elements on the rear window. That partially answers one of my questions. Now I just need to find a source, if any are available.
-
My questions below are relevant to the Avanti II. I need to replace the rear window seal in my 1963 Avanti. The window is also scratched in multiple places, so while I have the window out, I'd like to just go ahead and replace the glass. I'm not doing this soon, but I'd like to get it done in the next two years. Questions: What years, if any, did the Avanti II have a rear window defroster (wires or surface elements) in or on the glass? (I'm not concerned about originality. I want to make this car a three-season driver, and I'd like to have a functional defroster). If this glass is still available, what is the part number? Thank you.
-
No, sorry, nothing new to report. I haven't done any work on my Avanti since last fall. It's still sitting on the driveway on jack stands under a cover. I have a garage project I must finish before June 2. Once that's done, I can get back to work on the Avanti. One thing I did find at the SDC site is that someone found the rear disk brake caliper brackets that Jim designed hold the calipers in auch a way that the bleed valves are pointed down slightly, which might be creating a pocket inside the cylinder that's holding air away from the valves. When I get back at it, I'm planning to remove at least one of the caliper bolts so I can pivot the caliper so that the bleed valve is at top dead center. I also bought a new master cylinder from a local source. I think I may have damaged the seals inside one of the previous units when I experimented with the port to the rear brakes capped off. I would have attempted to rebuild it, but Raybestos does not sell replacement parts for it.
-
If one were to buy the correct well nuts for an Avanti side mirror from a Studebaker or Avanti parts vendor, what would be the correct part number to order?
-
"You may want to have a shop do the charging part if not experienced with it." Or take it to a state-licensed facility, if you live somewhere like Washington state, where it is now illegal to do any automotive air conditioning work unless it's done by a facility licensed by the state. In Washington the local auto parts stores can no longer sell cans of R134 or even do-it-yourself recharge / top-off kits, and it can't be shipped to residential addresses. We can buy it out of state and bring it back across the state line in a personal vehicle, but I'm sure that is also somehow illegal, and it's illegal to do the work in my driveway or inside my garage. Irritating. I have all the equipment to evacuate and service air conditioning, but I can't use it. What's really stupid, the national marketing office of a national chain auto parts store I frequent makes the local store put up posters advertising supplies to "get your air conditioning ready for summer", but the store can't sell any of it.
-
Also, I think the Avanti needs some kind of special inserts that fit in the holes in the fiberglass, and the screws that go through the mirror base screw into the centers of the inserts, not directly into the fiberglass.
-
Possibly distributor cap and rotor, maybe spark plug wire set. Enjoy your trip. Which island(s) will you see?
-
What is fishy about it? I bought my Avanti from the same seller, but not through Bring-a-Trailer. I inspected my Avanti in the seller's driveway so I knew what I was getting, where the photographs for this car were taken. Everything was smooth and legitimate.
-
Not only are the refrigerants different, the lubricating oils in the refrigerant lines to lubricate the compressor are different, too. R12 uses mineral oil. R134 uses polyalkylene glycol (PAG). If you convert from R12 to R134, any parts that are retained for re-use must be thoroughly flushed with an appropriate solvent to remove all the mineral oil, something that will cut and remove the mineral oil without damaging the parts. About 25-30 years ago I converted the A/C system in a 1993 Ford Crown Victoria to R134. The kit came with everything except the evaporator. Since I didn't replace it (buried inside the dashboard) I flushed it with some kind of alcohol and blew out the alcohol with compressed air. I don't remember what alcohol I used. The conversion worked well, and it was still cooling when we sold the car in 2006.
-
Deal. Send me a private message with your name and address. I'll break them down into manageable bundles and box them up in multiple boxes for shipping.
-
The Studebaker Lark I sold last year was originally equipped with power steering from the factory, but sometime before I bought it, it was converted to standard steering. To make steering at low speed a bit easier, I learned to anticipate which way I was planning to turn after a stop. I did some of the turn while the car was still rolling, stopped, then began the rest of the turn when I started roll and avoided turning the wheel when the car was stationary.
-
For those of you who collect physical ephemera, I am giving away an almost complete set of AOAI magazines, from volume 1 issue 1 up to about 2017 or so. They are currently in three large boxes. When these were given to me a few years ago, I went through all of them and put them in order. A few individual issues are missing. There are some duplicates. These are free to anyone who wants them. No shipping. I'll drive up to 3 hours one way from Seattle to meet you somewhere halfway to transfer ownership.
-
Do they sell radiators specific to the Avanti, or did you have to pick one for a different car and make it work? What was the part number you ordered?
-
Wow, very nice. The interior looks great.
-
There's a 1963 Avanti R1 on Bring-A-Trailer. https://bringatrailer.com/listing/1963-studebaker-avanti-69/
-
I believe Ford has outsourced all their production records from 1967 through 2020 to Marti Auto Works.
-
It's looped inside the pillar and held with something like a clip. When I replaced my vent hose I cut the visible ends just below the pillar and shoved it up inside the pillar to get it out of the way. If I ever remove the interior lining of the pillar, I'll remove the clip and cut portion of the hose.
-
The large hole in the middle can be plugged with a metal or rubber body plug of the same diameter. I used a metal plug to make it less likely for a mouse to chew through it. The smaller hole to the right of it is where the gas tank vent tube passes through the body.
-
As pictured in post 5, deluxe trim had smooth, perforated vinyl inserts on the seat backs and bottoms. The regal trim had pleated vinyl with no perforations.
-
Thanks. He spent most of his time at Studebaker working in building 84. This is the two of us outside buildings 84 and 113 in September 2021. My youngest daughter and I stopped in South Bend to visit my parents after driving my '62 Lark Daytona hardtop to the SDC International Meet in Indianapolis. That was a long, hot trip. He passed about six weeks later, and my mother about 10 weeks after him.
-
Wow, a 16 year old boy with a new Avanti. I'm speechless. Just...wow.
-
Yes. My father worked in the auto assembly building in South Bend. He was in the Production Control department. One of his duties was to collect copies of the production orders as the cars came down the assembly line and turn them in so they could be filed.
-
Regarding my response in post 3 above, this is a photograph of the production order that was found in the dashboard of our chapter member's 1961 Cruiser. In the bottom center it says "Production Order - Body Set". In the bottom right corner, it says "Instrument Panel Copy". This does not specifically answer the question in post 1 above.
-
63stick, it's yours. I just sent you a Private Message requesting your mailing address. For your privacy, please do not post it in this thread.
-
One of our local SDC chapter members is selling a 1961 Lark Cruiser. He said he found a copy of the build sheet tucked up into the dashboard near the glove box. It certainly looks like it was in the car for quite a few years.